[TECHNICAL INFORMATION]
RECYCLING PET MODIFIER
AR-P-1100
Introduction
PET bottle recycling has been a focus of attention in recent years in accordance
with increasing demand for PET with its versatile character, and enforcement
of The Containers and Packaging Recycling Law (Japan) in 1997. Collection
of used PET bottles (recycling PET) has been then increased every year
as shown in the table 1 below.
Table 1. Collection of used PET bottles
Municipalities Collection |
Sep. 2005
Japan PET Bottle Association |
@@ |
Volume of collected
bottles(ton) |
Production
(ton) |
Rate of collection
(%) |
1995 |
2,594 |
142,110 |
1.8 |
1996 |
5,094 |
172,902 |
2.9 |
1997 |
21,361 |
218,806 |
9.8 |
1998 |
47,620 |
281,927 |
16.9 |
1999 |
75,811 |
332,202 |
22.8 |
2000 |
124,873 |
361,944 |
34.5 |
2001 |
161,651 |
402,727 |
40.1 |
2002 |
188,194 |
412,565 |
45.6 |
2003 |
211,753 |
436,556 |
48.5 |
2004 |
238,469 |
513,712 |
46.4 |
Total Collection |
@@ |
Volume of collected
bottles(ton) |
Production
(ton) |
Rate of collection
(%) |
2001 |
177,186 |
402,727 |
44 |
2002 |
220,256 |
412,565 |
53.4 |
2003 |
226,405 |
436,556 |
61 |
2004 |
319,893 |
513,712 |
62.3 |
Remarks :
Production is weight of Recycling designated PET bottles@(soft drinks,
soy sauce and liquors) |
|
Recycling PET was mainly reused as fibers and sheets as shown in the table
2. It is because such characteristics of recycling PET limited applicable
molding method as the molecular weight reduction in molding where the melt
viscosity might be decreased, and an extreme decrease in the impact strength
without drawing. Fibers and sheets made by recycling PET, however, saturated
the market already, so that the most of collected PET bottles began to
be thrown out before recycling.
Under such circumstances, development of applicable method of injection
and profile extrusion molding has been an essential issue for recycling
PET.
Table 2. Trend of recycled PET's market capacity in Japan
Sep. 2005
unit : thousand tons |
Market |
1997 |
1998 |
1999 |
2000 |
2001 |
2002 |
2003 |
2004 |
Fibers |
6.1 |
16.9 |
25.2 |
38.3 |
48.7 |
58.9 |
57.4 |
63.6 |
Sheet |
1.1 |
5.2 |
11.5 |
23.4 |
37.5 |
45.6 |
50 |
54.6 |
Bottle |
0.8 |
0.2 |
0.2 |
0.3 |
0.4 |
0.6 |
11.3 |
23.3 |
Molding |
0.4 |
1.3 |
2.5 |
3.8 |
5.3 |
5.3 |
3.9 |
4.2 |
Others |
0 |
0.3 |
0.3 |
2.7 |
3 |
2 |
1.6 |
2 |
Total |
8.4 |
23.9 |
39.6 |
68.6 |
94.9 |
112.5 |
124.3 |
147.7 |
There is summation data by Japan Containers and Packaging Recycling Association,
although these values do not accurately reflect total market size in Japan. |
|
Problem with recycling PET
In molding recycling PET, hydrolysis that may reduce the molecular weight
is an unavoidable action when strictly controlling water. Hydrolysis of
Recycling PET proceeds according to the following structure.
 |
Such molecular weight reduction of recycling PET is the prime cause of
a decrease in impact strength of a molded part without drawing process.
And a decrease in the melt viscosity leads to running from nozzle and defective
appearance in injection molding, and makes it difficult to be diluted for
size enlargement in profile extrusion molding.
In order to solve these problems, we have developed and commercialized
"AR-P-1100", recycling PET modifier, making use of the technology
of styrene copolymer.
Recycling PET modifier AR-P-1100
AR-P-1100 may inhibit hydrolysis of recycling PET in molding to forcefully
make it high molecules. Such main problems in using recycling PET as the
decrease in impact strength and melt viscosity can be solved by adding
a little amount of AR-P-1100. Recycling PET is modified by AR-P-1100 where
elastic elements are uniformly dispersed in reactive parts so that they
are polymerized. Interfacial adhesion between recycling PET and elastomer
is reinforced, and impact strength is improved since elastic particles
restrain crack spreading that likely to occur continuously and in laminae.
AR-P-1100 improves the melt viscosity of recycling PET, of which modification
is entwinement between recycling PET and high-molecule-weight elastomers
that are scattered in molecular chains being steric by graft polymerization
in straight chains with reactive parts.
Additionally, AP-P-1100 is resistant to heat that can be blended with recycling
PET and dried together without melting and softening.
General features and characteristics of AR-P-1100 are described as follows.
Table 3. Physical properties
Items |
Test method |
Unit |
AR-P-1100 |
Hardness |
JIS K 7215 D |
-- |
39 |
Specific gravity |
JIS K 7112 |
-- |
0.9 |
MFR |
JIS K 7210 (8) |
g/10 min. |
1.8 |
Tensile strength |
JIS K 6251 |
MPa |
7.2 |
100% modulus |
JIS K 6251 |
MPa |
7 |
Elongation |
JIS K 6251 |
% |
160 |
Tear strength |
JIS K 6252 |
KN/m |
69.6 |
* MFR (8) 200 - 5,000g
Note) values are represented for your information without guarantee |
|
Table 4. Effect to recycling PET
Recycling PET
AR-P-1000 |
100% |
95% |
90% |
85% |
@ |
5% |
10% |
15% |
|
|
|
|
|
|
Tensile yield strength (JIS K7113) |
Mpa |
61 |
55 |
49 |
46 |
Bending strength (JIS K7203) |
Mpa |
81 |
72 |
65 |
58 |
Bending elastic modulus (JIS K7203) |
Mpa |
2160 |
1950 |
1770 |
1670 |
Notich Izod impact strength |
kJ/m2 (23) |
1.4 |
3 |
5.1 |
5.3 |
(JIS K-7110) |
kJ/m2 (-10) |
1.2 |
3.2 |
5.2 |
5.2 |
Melt viscosity (shear rate 12.2 sec -1)@ |
Pa.s |
210 |
720 |
1460 |
2150 |
(shear rate 2430 sec -1)@ |
Pa.s |
95 |
130 |
110 |
110 |
Note) values are represented for your information without guarantee
Test condition:
sample made by injection molding; barrel temperature at 260; full flight
screw; die temperature at 30; predrying at 150 for 4 hours; test methods
conforming to JIS; melt viscosity measured by Capillary Rheometer at temperature
of 270; dice with 1 dia. X 10 mm t.; preheating time for 300 sec. |
|
The table 4 shows the effect of AR-P-1100 to physical properties of recycling
PET. Izod impact strength was markedly improved by adding a little amount
of AR-P-1100. Besides, molded part preserved low-temperature impact strength
inherent in PET and offered beautiful surface luster. Tensile yield strength,
bending strength, and bend elastic modulus inclined to decrease. However,
it can compete with general-purpose olefin in those values. Melt viscosity
was also improved dramatically in the lower shear rates, that can prevent
running from nozzle in injection molding, minimize inhaling of the air
caused by suck back, consequently prevent such defective molding as flash,
and stabilize measurement accuracy.
The improvement of melt viscosity by AR-P-1100 is also effective in extrusion
molding. The graph 1 shows the correlation between shear rates and melt
viscosity. By adding AR-P-1100 to recycling PET, the resin was viscous
enough in lower shear rates to be applicable to profile extrusion molding,
and became unsticky in higher shear rates mostly equivalent to pure recycling
PET.
AR-P-1100 makes recycling PET possible to be used in various molding methods
including injection and extrusion, producing such variation of melt viscosity
depending on shear rates.
Graph 1. Correlation between shear rate and viscosity of recycling PET
including AR-P-1100
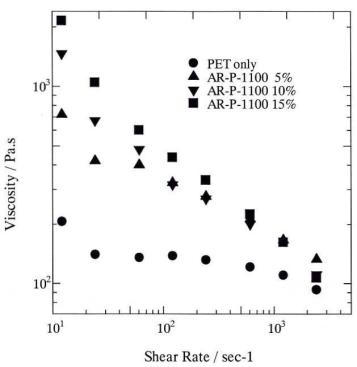
Dice diameter : 1 mm
Test temp. : 270
Pre-heating time : 300 sec.
Graph 2. Spiral fluidity of recycling PET including AR-P-1100
@
Injection pressure : 100 Mpa
Mold : 4 mm W x 3 mm T |
Viscosity improvement of recycling PET, one of function of AR-P-1100, represents
viscosity variation depending on shear rates. The resin with such varying
viscosity may flow well in injection molding. The graph 2 shows spiral
fluidity of recycling PET in case of adding AR-P-1100. The fluidity of
recycling PET including 10 - 15% AR-P-1100 is nearly equivalent to that
of recycling PET only when raising molding temperature by 10. This suggests
that not only modified recycling PET is versatile in a wide range of molding
conditions, but also it may retard heat degradation and hydrolysis of recycling
PET by setting a lower molding temperature.
Graph 3. Weatherability of finished product containing 15% AR-P-1100
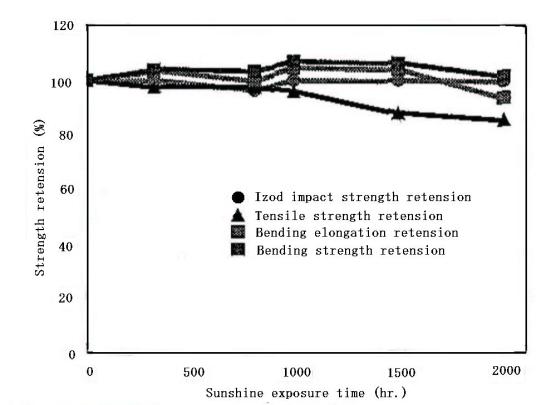 |
Tester : Suga Instrument's due cycle sunshine super long-life weather meter
WEL-SUN-DC
Test method : Continuous exposure test
Test conditions |
: Black panel (BP) temperature at 63 } 3
@Light source by sunshine carbon arc lamp
@Spray cycle by 18/120 min
|
Precaution
(1) AR-P-1100 requires no predrying
(2) Recycling PET tends to be muddy in milky white by
adding AR-P-1100.
Image 1. Viscosity improvement of recycling PET by adding AR-P-1100
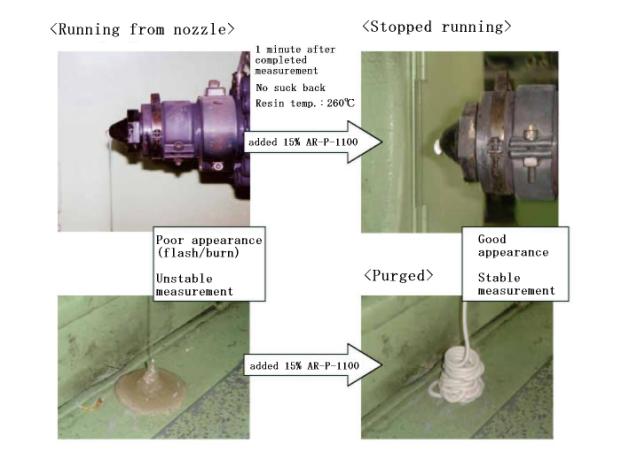 |
About PET resin
Modification of recycling PET achieved by AR-P-1100 may be materialized
by grasping characteristics of PET resin under optimum molding conditions.
Characteristics of PET resin in injection and extrusion molding are described
herein for your information.
PET main features are:
(1) The characteristics of PET resin may be influenced
by degree of crystallinity
(2) Requires a high molding temperature since the melting
point is 255
(3) May be degraded by progress of hydrolysis (heating)
(4) Requires strict water control (preliminary drying
at 130 - 140 for 3 - 4 hours)
Regarding (1), Change in its characteristics is shown in the table 5.
Table 5. PET resin characteristics depending on crystallinity
@@ |
Crystallized |
Uncrystallized |
Impact strength |
Very weak |
Weak |
Rigidity |
Very strong |
Strong |
Heat resistance |
Very strong |
Same as normal olefin |
Appearance |
White |
Transparent |
|
As aforementioned, recycling PET is very weak in impact strength. Therefore,
it is preferable to make a molded part with recycling PET before crystallizing.
In order to keep recycling PET uncrystallized while molding, it is necessary
to design a molded part with even radial thickness of 2 mm or less, and
to keep die temperature as low as possible and rapidly cool it.
Besides, it is important in injection molding to raise injection speed
as high as possible. Desirable mold structure is direct gate type with
a high taper rate with which such demerits of recycling PET as a short
gate seal time and a low shrinkage may be counterbalanced.
Because of characteristics described as (2) and (3), it is preferable that
molding should be carried out at a temperature around 255 with a shorter
residence time.
According to the above (4), it is necessary in injection molding to dry
recycling PET preliminarily by a dryer. On the contrary, it is confirmed
through actual equipment that by adding AR-P-1100, preliminary drying may
not be needed in profile extrusion molding. Though it involves a few limitations
including the need for a molding machine equipped with a vent (pressure
reduction and suction devices are not needed), AR-P-1100 may satisfy such
users' needs when newly introducing recycling PET as the reduction of the
total running cost and unnecessity of introducing a new machine.
PET resin is versatile because of its inherent properties in luster, impact
strength at low temperatures, chemical resistance, absence from toxicity,
and wheatherability. It is desired that AR-P-1100 may contribute to the
wide use of recycling PET.
Appendix
DESIRABLE MOLDING CONDITIONS IN USING OF RECYCLING PET WITH AR-P-1100
(1) DESIRABLE CONDITIONS OF INJECTION MOLDING
Preparation
Predrying:
Drying Temp. at 130 ` 140, Time for 3 ` 5 hours
Any of dryer equipped with a dehumidifier (or an agitator) is preferable
In case of a chamber dryer, thickness of material on the pats (plate containers)
of dryer should be 30 mm or so.
Molding conditions
Temperature:
Barrel temp. between 225 and 260; nozzle temp. 10 higher than barrel
temp.
Feed zone should be set as low as possible.
e.g., C1 at 150; C2 at 200; C3 at 260; C4 at 260; N at 270
In raising the temperature at feed zone, it is possible to measure incorrectly
since resin may become soft before screw, and adhere to the barrel.
Maximum molding temperature should be 280. In a high temperature exceeding
such maximum temperature, resin may be physically degraded as yellowing
or decomposing.
Plasticization and injection conditions:
Back-up pressure: set lower (between 2 and 10 kg/cm2)
Revolution: set faster (about 100 rpm) in order to minimize resin unevenness
by residence time difference; it is preferable to postpone measurement
in accordance with cooling time.
Suck back: minimize running from nozzle
Injection speed: set as fast as possible in order to minimize defects of
finished product
Injection pressure: set higher in accordance with injection speed
Follow-up pressure: same pressure as general-purpose PET; pressure keeping
time should be re-set for every mold according to gate diameter and shape;
since PET may become a gate seal soon, it is hard to release molded parts
from the mold if pressure keeping time is too long.
Screw type: general-purpose or full flight type screw is sufficient; a
check ring (chuck ring) is needed.
Other notes: it is preferable to cool nozzle down to prevent cold slag,
and to withdraw nozzle every batch to prevent die from heating.
Mold:
Mold temperature: below 40; it is preferable to use a chiller to cool
die down so that impact strength of molded part may be improved
Cooling time: roughly same time as PVC
Other notes (for your information)
Preferable gate type is a direct gate with a taper of about 3 degrees.
Ideally, the gate length should be shorter in order not to make a large
gate diameter. Part strength near the gate may be poor or break-off may
occur If the gate diameter is too large. Using a direct gate, it is possible
to carry out molding smoothly.
L/t is limited by 250. In using general-purpose resin, L/t is extended
by raising molding and die temperature. In using PET, however, such temperature
control may result in vain. It is better to recondition hardware including
gate replacement.
(2) DESIRABLE CONDITIONS OF EXTRUSION MOLDING
Preparation
Predrying: basically it is unnecessary to predry. However, predrying at
140 may improve a little viscosity of resin and impact strength of molded
part.
Molding conditions
Temperature:
Barrel temp. between 230 and 270; In a vent type machine, raise temperature
before vent to accelerate exhaustion, so that physical properties of resin
may be improved.
It is easy to size in a lower adapter and dies
e.g., C1 at 230; C2 at 250; C3 at 265; C4 at 260; AD at 250; D at
240
In starting up, adapter and dies temperature should be 260, and lower
it gradually; If set as the above example from the beginning, it is possible
to raise back-up pressure rapidly.
Maximum molding temperature should be 280. In a high temperature exceeding
such maximum temperature, resin may be physically degraded as yellowing
or decomposing.
Revolution: set revolution as fast as possible (about 100 rpm) in order
to minimize degradation of physical properties of resin for a long residence
time.
Machine specification:
A vent type machine equipped with a vent and 2 shafts is preferable. When
using a machine with one shaft without vent, back-up pressure should be
higher by inserting a mesh.
Screw: L/D = 25 to 30; a screw with high kneading disc is preferable, although
a general-purpose screw design can be used.
|